The launch of the new Discovery brings with it the announcement of a new
diesel engine, Td5. This will be a major building block in the future success of the
company, as
not only will it be powering the new Discovery, it will also be replacing the Tdi in all
UK-built Defenders.Five cylinder engines are unusual, five cylinder diesels rarer still
and totally new engines for Land Rover products - well Td5 is the very first! All previous
Land Rover engines have been adapted or derived from an existing unit and on those grounds
alone this engine warrants closer examination.
The project began in 1993 after the then Rover Group management had decided to produce
a new range of engines that would meet all of the group's diesel engine requirements. With
the company still under the ownership of BAe at that time, investment funds were limited.
To reduce development and production costs, it was planned that the programme would
spawn a number of modular engines of 4, 5 and 6 cylinders and of varying capacities.
Before design work started in earnest, the company examined all of its competitor engines
from around the world as well as re-examining the lessons it had learnt from its own L
series and Tdi units.
Carrying the codename of Project Storm, preliminary design work could begin. Central to
the development of Storm were the impending EEC11 emissions legislation. Land Rover knew
that its existing Tdi unit was unable to meet the new requirements. This coupled with
customer demands for greater refinement, lower running costs, better fuel economy and the
desire to adopt new production techniques to improve quality, led the company to the
conclusion that the best way forward would be with a totally new design.
With the advantage of having the proverbial clean sheet of paper, Land Rover's
engineers have adopted some interesting and radical solutions to the problems that they
faced. Fundamental to the success of the engine in meeting its emissions and economy
targets would be the method of fuel injection used. Land Rover have adopted the very
latest technology available, Electronic Unit Injectors (EUI). Already proven around the world in larger
commercial diesel engines, this is their first application in a 4x4, and a small capacity
engine. Especially developed by Lucas Varity for Td5, these units combine the role of
traditional high pressure pump and injector into a single unit.
A major part of the design effort in Td5 went into the cylinder head, as this had to
accommodate the needs of the EUI technology. Produced in LM25 aluminium alloy to give
maximum stiffness and high clamping loads, the inlet and exhaust porting profiles have
been developed by AVL of Austria to maximise gas flow. An overhead camshaft, produced by
BMW for Land Rover, has three lobes per cylinder, two operate the valves, one powers the
EUI. Because of this extra load, the camshaft is driven by an automatically tensioned
duplex chain drive from the crankshaft. Also built into the cylinder head are the fuel
flow galleries which supply the EUI and return the excess fuel to the tank.
The EUI themselves are located in the cylinder head directly above the combustion
chamber. Fuel is allowed to flow from the cylinder head fuel galleries into the EUI and
out again via an electronically controlled spill valve. The EUI becomes primed, with the
fuel flowing into a chamber below the injector plunger. The engine control module (ECM)
then instructs the spill valve to close. The plunger, which is driven from the camshaft,
starts its downward stroke causing pressure to build in the injector passages.
At a
predetermined pressure the nozzle opens, in two stages, first pre-lift and then full-lift
and the fuel is injected. This two stage process lowers the initial rate of injection,
giving quieter and cleaner combustion.
Under instructions from the ECM the spill valve opens, allowing the pressure to
collapse and thus the nozzle closes. This system allows for very precise timing of the
injection, its duration, the quantity of fuel used and allows incredibly high injection
pressures of around 1500 bar, compared to the 300 series Tdi which runs at 300 bar.
Artwork in the galleries
An entirely new method of fuel supply and return has also been developed for Td5. Fuel
is initially passed from the tank by a two stage submerged electric pump, firstly at low
pressure, to a canister type fuel filter located on the vehicle's chassis. This filter is
ultra fine and is able to retain particles in the 3 to 5 micron range. Fuel is then
returned to the second stage of the pump where the cleaned fuel is pressurised to 4 bar
and sent on to the engine. On arrival at the cylinder head the fuel passes through a final
filter, a temperature sensor and a pressure relief valve. This valve controls the pressure
feed to the injectors by regulating the amount of fuel entering the return system.
The return system itself is a work of art. As we have seen the fuel galleries form an
integral part of the cylinder head with the consequence that the returning fuel acts as a
heat sink and the overall temperature of the bulk fuel supply in the tank would gradually
rise. As the EUI system works best with 'cool fuel' returning, fuel is passed through a
cooler unit mounted on the side of the inlet manifold. This has its own dedicated coolant
circulation to a separate small diameter cooling tube mounted on the main radiator.
Because this tube is narrow it constrains the flow and super cools the coolant, providing
a constant heat reduction to the fuel.
As a final filtration the returning fuel passes through a restrictor which is similar
to those used in hospitals. A micro-porus filter akin to those used in blood drips allows
air to pass but not fuel thus de-bubbling the fuel as it is passed back into the tank.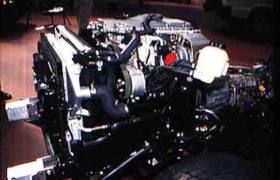
The cast iron Td5 cylinder block is of a new design although it is closely related to
the existing L series engine with which it shares a number of features. With a cylinder
spacing of 94mm and a bore and stroke of 84.45 x 88.95mm, the engine has been designed to
be processed on the same all new block-machining line at Solihull as the L series.
To give maximum stiffness to the block, it has vertical box sections cast into the
sides, these also allow a rapid oil return route. The cylinder head is bolted to the block
with 'through bolt fixings' which allow maximum clamping loads.
A six bearing cast iron crankshaft with five balance weights to ensure smooth running
is fitted. This in turn drives a dual mass flywheel. This has two masses connected by
internal spring elements, which help to smooth out the individual cylinder combustion
pulses.
Additional stiffness at the bottom of the block comes from an aluminium ladder frame
which is fitted with an integral oil pump and has oil flow galleries cast into it. These
supply the main oil channels in the block and the oil squirt jets that cool the pistons.
An oilman's nightmare
One of the main aims of the Td5 programme was to reduce overall running costs by
extending the oil change intervals. To meet that requirement the engine has been equipped
with a novel approach to oil filtration in having two filters. Primary filtration
comes from a normal full flow paper element. A second centrifugal filter is also fitted.
This is located in a small 'pot' by the exhaust manifold. Two fine oil jets spin the
centre canister at up to 15,000 rpm causing particles to be retained in the inner wall of
the canister. As a measure of how effective this is, recommended oil change intervals are
now every 12,000 miles, the main filter changes are at 36,000 miles and the canister
filter needs a change at 12,000 miles.
As is the standard today, Td5 is both turbocharged and intercooled. Air is drawn into
the filter from an underwing mounted nozzle to maximise air flow and the vehicle's deep
water wading capacity. Air is passed through a new Garrett GT20 turbocharger, developed
specifically for Td5. It has a 47mm diameter turbine wheel and a 52mm compressor,
operating at compression ratios of 2.4:1 and at speeds of up to 180,000 rpm. A new system
of electronic wastegate modulation is used and the intercooler is of a new lightweight
design.
The cooling system uses a new lightweight cross flow radiator and moulded 18 inch one
piece cooling fan, with an integral moulded-in viscous drive. The system has been
developed to provide fast engine warm up and cabin heat as quickly as possible.
Finally a crankshaft driven serpentine poly-vee belt provides power to the
engine-driven ancillaries, alternator, water and power steering pumps and where fitted the
air-conditioning compressor and the active cornering enhancement hydraulic pump. Td5 is
finished off with the fitting of a styled acoustic cover over the top of the engine and an
undertray which both combine to reduce noise levels by 8 to 10 dBA.
Under new management
While Storm was being developed another project was taking shape, without which Td5
would be a non-runner. Project Thunder was the title given to the programme to develop the
Engine Control Module (ECM). More powerful than any previous engine management system used
by the Rover Group for any of its powertrains, the unit monitors the demands being placed
upon the engine from a variety of sensors and adjusts the fuelling of the EUIs to respond.
As the engine is fully electronic, a drive by wire system is used to translate the
throttle position. Pressing the accelerator sends a signal to the ECM and that commands more power from
the engine. However the electronics can adapt the throttle depending on whether high or
low range is engaged. Fast Throttle Control (FTC) makes most of the power accessible in
the first 30 percent of the pedal travel in high range. Select low box and the throttle
changes to a long travel setting to aid gentle power changes for maximum off-road
performance.
The end result of all this electronics and engineering is a supremely smooth and
capable engine. As expected the engine has all the stump pulling power we have come to
expect from Land Rover's recent engines. Power is increased to 136 bhp for Td5 compared to
111 bhp for Tdi and maximum torque increases to 221 lb.ft. The torque available is also
excellent, the maximum is available at 1950 rpm, with 90 percent available at a mere 1450
rpm, while the torque spread is also improved with 80 percent of maximum on tap from 1300
to 3900 rpm.
With the introduction of Freelander, Land Rover signalled that it was
prepared to move into new markets. New Discovery and Td5 show
that they haven't forgotten their roots and can still build capable,
exciting and advanced 4x4s.
   
|